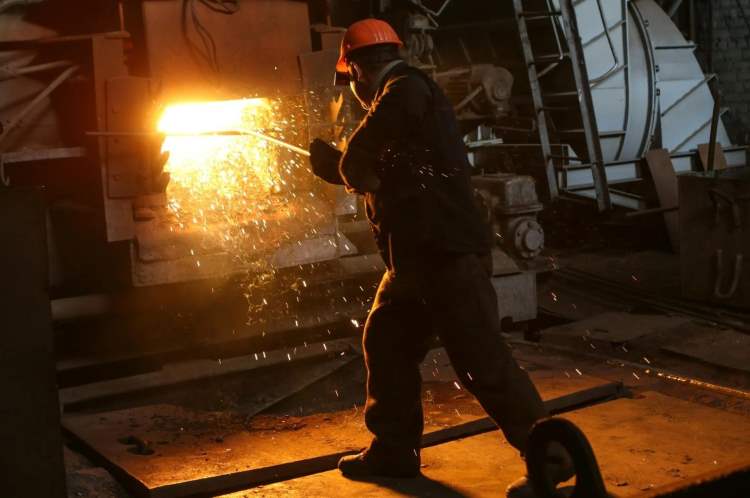
India’s efforts to become a global manufacturing hub may finally be showing some results. With concerted government efforts to promote domestic industry, key metrics reflecting the sector’s efficiency and performance are steadily improving—offering cautious optimism of a private capital expenditure revival in the months ahead.
A particularly promising indicator is the gestation rate of manufacturing projects—a measure of time efficiency relative to project cost. Defined by the Centre for Monitoring Indian Economy (CMIE) as the number of months from project announcement to completion divided by the project cost (in Rs 100 crore units), this metric reflects how quickly capital is being deployed. A lower rate signals higher execution efficiency and quicker returns on investment—factors critical for attracting private sector capex at a time when the government is seeking to share the fiscal burden.
READ | Health diplomacy under strain: Power, politics and the future of collaboration
In FY 2024–25, India’s manufacturing gestation rate stood at 9.17 months per Rs 100 crore—the best in half a decade. For context, this figure was 10.33 in FY19 and 12.58 in the two years preceding it. The improvement is emblematic of a broader shift in India’s manufacturing sector, driven by a changing global supply chain environment and a series of targeted incentives aimed at select industries.
Consumer durables take the lead
Among the sectors leading this shift are consumer durables, transport equipment, agro-based industries, and machinery. The consumer goods sector, in particular, has seen dramatic changes. India, which earlier relied heavily on imports for appliances like mobile phones, air conditioners, and washing machines, is now seeing rising domestic investments in these areas. The shift is driven by a mix of strategic supply chain diversification and policy measures such as production-linked incentive (PLI) schemes.
Mobile phone manufacturing hubs in states like Tamil Nadu are examples of how streamlined approvals and targeted incentives have reduced project gestation times and enhanced investor confidence. Analysts believe this trend can drive a broader revival in private capex, fuelling a virtuous cycle of production and demand.
Headwinds for metals, textiles, and mining
However, the picture is far from uniformly positive. Key sectors like metals, textiles, and non-manufacturing industries such as mining, electricity, construction, and real estate have witnessed a worrying spike in gestation rates. In fact, the rate for the broader private sector—including non-manufacturing—has hit a 20-year high.
Among these, mining has seen the steepest increase in project delays, followed by real estate and construction. Complex land acquisition processes, environmental clearance hurdles, and a lack of streamlined regulatory frameworks continue to plague these sectors.
In contrast, countries like China—with their advanced infrastructure, centralised approvals, and skilled workforce—report gestation rates as low as 6–7 months per Rs 100 crore equivalent for comparable projects. Although overcapacity in sectors like steel and textiles has begun to create drag even for China, its manufacturing machine still outpaces India’s by a wide margin.
Structural challenges linger
Despite the momentum, structural issues continue to weigh on investor sentiment. Long-standing concerns about regulatory unpredictability, especially around decarbonisation and emerging trade norms such as the European Union’s Carbon Border Adjustment Mechanism (CBAM), have dented confidence among major investors in heavy industries like oil and gas and metals.
These sectors—historically magnets for private capex—now face an uncertain future as they recalibrate business models to align with global climate mandates. Indian firms navigating these headwinds find themselves in a policy limbo, with no clear long-term regulatory guidance. This has led many to adopt a wait-and-watch stance, further delaying investments critical for industrial growth.
Additionally, India faces stiff competition from countries like Vietnam and Mexico. While Vietnam offers cost advantages in labour and efficiency, Mexico benefits from geographical proximity to key markets like the United States. India must carve out its own unique value proposition to remain competitive.
Can India catch up
While catching up with China’s manufacturing prowess may take decades, India’s recent progress is promising. But sustaining this momentum will require more than just improved gestation metrics.
Policymakers must double down on complementary reforms—particularly in easing land acquisition, reducing red tape, and modernising infrastructure. The adoption of lean manufacturing practices, aimed at reducing waste and boosting productivity, can further streamline operations. Meanwhile, integrating advanced technologies such as automation, artificial intelligence (AI), and Internet of Things (IoT) under the Industry 4.0 umbrella can dramatically improve manufacturing precision and cost-efficiency.
Building resilient and diversified supply chains is also essential. The COVID-19 pandemic and subsequent geopolitical disruptions exposed the fragility of global supply networks, especially in critical sectors like semiconductors. India must act swiftly to insulate its manufacturing sector from similar shocks in the future.
The gestation rate improvements signal that the country is on the right path, but without structural reforms and long-term policy clarity, the private sector’s appetite for large-scale investment will remain limited.
India’s manufacturing journey is a marathon, not a sprint. The coming years will test whether the nation can translate promise into performance—and whether it can build an ecosystem robust enough to rival China’s industrial dominance.