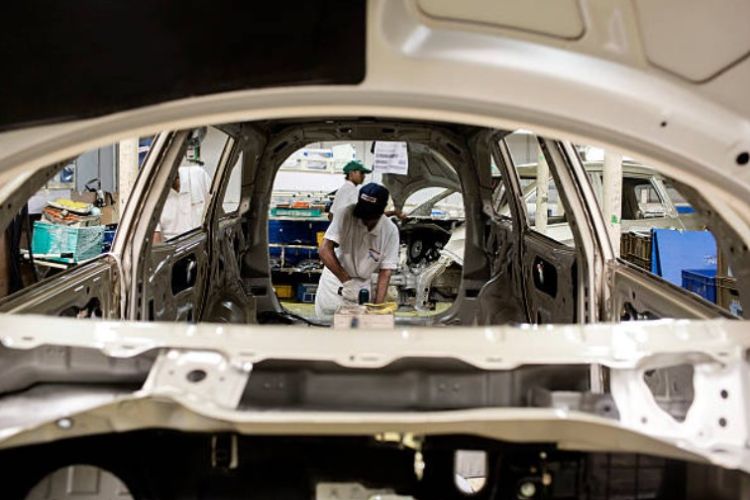
India’s auto component industry, long seen as a pillar of the country’s industrial base, is facing global uncertainties, rising protectionism, and evolving consumer demand. While the sector has reaped the benefits of India’s rapid economic growth in recent years—bolstered by infrastructure investments, rising disposable incomes, and government-led manufacturing incentives—it now finds itself contending with fresh challenges.
The renewed trade tensions driven by US President Donald Trump’s tariff agenda have unsettled global supply chains, with ripple effects reaching India’s manufacturing corridors. For the auto component sector, which had been eyeing robust growth, the outlook for FY25 has moderated to a projected 7–9%, as international headwinds dampen demand and cloud prospects.
READ | Europe must prepare for a NATO without America
In response, Indian manufacturers are recalibrating their strategies. Industry leaders are placing renewed emphasis on localisation to anchor supply chains domestically and diversification to reduce their exposure to volatile markets. Companies such as Kinetic Engineering and Samvardhana Motherson International Ltd. (SAMIL) are proactively forging long-term partnerships and prioritising a technology-forward, risk-aware approach to global expansion.
According to industry executives, imports are now largely restricted to niche, highly specialised components not yet manufactured in India. Firms that have pursued aggressive localisation strategies report minimal exposure to tariff-related disruptions, underscoring the importance of self-reliance in an era of uncertain trade policy.
One notable shift triggered by the tariff war is the increased engagement between Indian suppliers and global original equipment manufacturers (OEMs). Companies are now co-developing contingency plans, conducting joint feasibility studies, and investing in future-ready production pipelines. Given that automobile programmes typically span seven years—encompassing prototyping, testing, and validation—this long-term horizon provides firms with a buffer to absorb shocks and adapt to shifting trade dynamics.
Yet, diversification is easier said than done. Indian suppliers are venturing into new geographies as a hedge against subdued global growth and softening domestic demand, but the transition is neither quick nor cheap. Developing customised components for new OEMs takes anywhere between 8 and 24 months and requires significant upfront investment.
There is also a deeper vulnerability that the industry must confront: India’s heavy dependence on imported auto components, particularly from China. In FY24, India imported over $20 billion worth of auto parts, with China alone accounting for 23% of this total. Even with the prospect of favourable tariffs from the US, experts caution that India may struggle to substitute Chinese imports at competitive prices, given the current cost structures and scale advantages that Chinese manufacturers enjoy.
Despite these hurdles, industry leaders remain cautiously optimistic. Many view the present churn as an inflection point that could ultimately position India as a net beneficiary of the ongoing global trade realignment. With the US market increasingly looking inward and China facing mounting geopolitical resistance, Indian suppliers have an opportunity to plug into alternative value chains—particularly in emerging markets across Africa and Southeast Asia.
Outlook for auto component industry
The long-term potential is significant. The auto component industry currently accounts for 2.3% of India’s GDP and employs more than 1.5 million people directly. Under the Automotive Mission Plan (2016–26), the sector is projected to add another 3.2 million direct jobs by 2026.
Recent data underscore this momentum. India’s auto component exports surged from $7.4 billion in FY21 to $12.8 billion in FY24—a 73% increase over three years. This rebound from pandemic-era lows reflects not just global demand recovery, but also India’s growing credibility as a high-quality, cost-effective manufacturing destination.
The bulk of these exports comprise Drive Transmission Systems, Engine Components, and Electrical and Electronics parts, which together account for over half of India’s total component exports. North America and Europe remain the largest export markets, together absorbing nearly two-thirds of India’s outbound shipments in this sector.
India’s geographical proximity to Africa and Southeast Asia, where automotive manufacturing and consumption are on the rise, provides another layer of opportunity. As these markets mature, India is well-positioned to expand its footprint, provided it can maintain cost competitiveness and meet evolving quality benchmarks.
Still, realising this potential will require more than entrepreneurial agility. Industry stakeholders have called for targeted policy interventions to sustain momentum—ranging from production-linked incentives and R&D support to streamlined trade agreements that ease access to new markets. The NITI Aayog, in a recent report, affirmed that India’s strong manufacturing base and cost advantages could eventually make it a global leader in the auto component segment—if the right enablers are in place.
The next phase of growth for the sector will not come without risk. But if India can seize this moment of disruption to strengthen its supply chain, reduce overdependence on specific geographies, and unlock new trade relationships, the auto component industry may well become a cornerstone of the country’s ambitions to become a global manufacturing powerhouse.