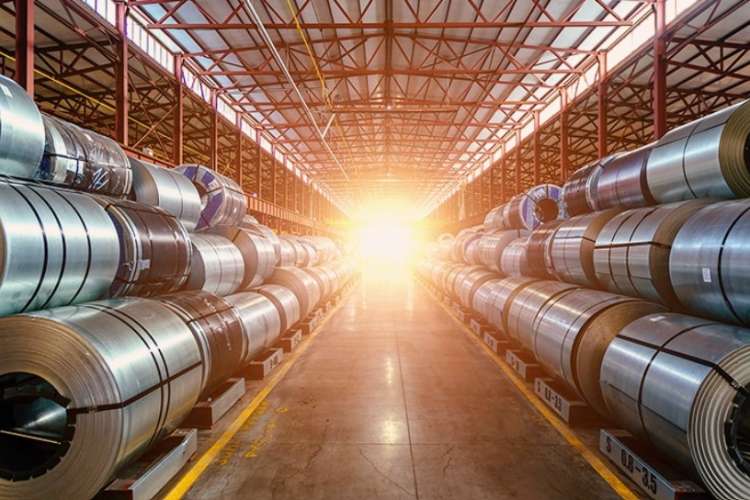
Decarbonising India’s Steel industry: Induction furnaces (IFs) and electric arc furnaces (EAFs) play a major role in India’s steel sector, producing approximately 40% of the nation’s crude steel and accounting for 43% of its steel production capacity in 2023–24. These plants are numerous but small in capacity, with a typical facility producing less than one million tonnes annually. India currently hosts over 1,000 such plants, employing 1.8 million workers and contributing significantly to economic growth despite their fragmented nature.
However, these plants face challenges due to higher energy and emissions intensity compared to other steelmaking methods. Despite this, IF-EAFs hold potential to align with low-emissions steel targets, though their transition pathways remain underexplored. This op-ed delves into the decarbonisation potential of IF-EAFs and their critical role in India’s steelmaking future.
READ | Sustainability in the digital age: Lessons from across the global divide
Steelmaking routes in India
Steelmaking can be broadly categorised into two routes, as defined by the World Steel Association: primary steelmaking and secondary steelmaking. Primary steelmaking converts iron ore into steel, typically through the blast furnace-basic oxygen furnace (BF-BOF) route. Secondary steelmaking, on the other hand, utilises recycled steel as a raw material, commonly through the EAF route.
Globally, primary steel is predominantly produced via BF-BOF. In India, however, the DRI-EAF route complements BF-BOF, with IF-EAFs enabling India to become a global leader in direct reduced iron (DRI) or sponge iron production. Notably, India operates 344 coal-based DRI units, while 1,032 IF units recycle 68% of total steel scrap for crude steel production.
In the past five years, India’s crude steel production has grown by 35 million tonnes, with IF-EAFs contributing half of this increase. As India aims to reach a steel production capacity of 300 million tonnes by 2030–31, these smaller-scale plants will play an instrumental role in meeting the target while necessitating decarbonisation.
Decarbonisation: An imperative for steel sector
The steel industry contributes 10–12% of India’s total emissions, with energy and emission intensity higher than the global average. Decarbonisation of the sector is critical for India to meet its net-zero emissions target by 2070. To achieve this, India’s steel sector must adopt low-carbon technologies, including increased use of scrap and green hydrogen-powered DRI. Green hydrogen offers the dual benefits of reducing reliance on coal and supporting renewable energy-powered EAFs.
Energy efficiency improvements, such as modernising kilns and operational processes, can further reduce emissions while cutting costs. Carbon capture, utilisation, and storage (CCUS) also holds promise but faces significant challenges in terms of cost and feasibility. Initiatives like boosting green hydrogen production align with these efforts and position the steel sector to capitalise on the growing global demand for low-emission steel. Moreover, compliance with international regulations, such as the EU’s Carbon Border Adjustment Mechanism (CBAM), is essential to maintain competitiveness.
Challenges in transitioning to green steel
The path to decarbonising India’s steel sector is fraught with challenges. One significant hurdle is the high capital investment required for adopting low-carbon technologies, such as green hydrogen-powered DRI and renewable energy-based EAFs. Smaller IF-EAF operators, which traditionally operate on low margins, often struggle with financing and equipment upgrades. The fragmented nature of the industry further complicates the implementation of consistent emission-reduction measures, leading to inconsistencies in technology adoption and operational practices.
Another challenge is access to high-quality raw materials, particularly scrap steel, which is hindered by inadequate recycling policies and infrastructure. Existing coal-based plants also face difficulties in upgrading or replacing older equipment to integrate CCUS technologies, which are both costly and complex. Furthermore, the shift to advanced technologies necessitates workforce skill upgrades, ensuring that employees can effectively operate new systems.
Opportunities in IF-EAFs
Despite these challenges, IF-EAFs are uniquely positioned to drive the transition toward low-carbon steel production. Their existing familiarity with DRI and recycled steel gives them an advantage in adopting green hydrogen technologies. The smaller scale of these operations enables them to conduct cost-effective pilot projects, which can be tailored to India’s unique infrastructure and climate conditions.
Moreover, the fragmented structure of IF-EAFs, often seen as a drawback, can be leveraged for decentralised decarbonisation strategies. This allows for region-specific solutions that address local challenges while fostering innovation. Successful incremental changes in operations can serve as models for the rest of the industry, accelerating the adoption of low-emission practices across the sector.
IF-EAFs also play a critical role in enhancing India’s export potential. By aligning with international environmental standards and adopting sustainable practices, these plants can strengthen their position in global markets. As the industry transitions, workforce training and development will further improve capabilities, ensuring a smooth and inclusive transition
A green future for India’s steel sector
To fully exploit the potential of IF-EAFs, India must address key issues. First, affordable access to green hydrogen and renewable energy is essential. Financial incentives and low-cost financing options can support smaller operators in adopting advanced technologies. Robust recycling policies and infrastructure must also be developed to ensure a steady supply of high-quality scrap steel. Finally, significant investments in workforce training and skill development are needed to manage the transition effectively.
India’s steel sector stands at a critical juncture, with IF-EAFs positioned to lead the decarbonisation movement. Their operational flexibility, familiarity with DRI technologies, and capacity for localised solutions make them ideal for spearheading the transition to green steel. Strategic investments in these industries can drive sustainable growth, align with international climate goals, and enhance India’s competitiveness in the global steel market.
By placing IF-EAFs at the heart of its decarbonisation strategy, India can achieve its production and environmental targets while fostering a resilient, innovative, and inclusive steel sector. This transformation will not only support India’s manufacturing goals under the Make in India initiative but also position the country as a global leader in low-emission steel production.
Garapati Tarun Kumar is an MBA student, and Mousami Prasad Assistant Professor at Department of Management Sciences, IIT Kanpur.